The rise of AI industrial robotics experienced record double-digit expansion in various countries in 2014 and 2015, but such large scale segments i.e. ‘industrial’ versus ‘medical’ or ‘military’, were more or less one amalgam of parts a couple of decades ago. Examples of medical and military applications can be found in our updated machine learning in robotics guide. There was a time before the early 1980s when it was possible for AI researchers to keep up with all that was going on in the AI and the robotics industry as a whole, but it seems the tides had changed by 1982.
At that time, in a column out of MIT’s AI Laboratory, Tomas Lozano-Perez noted that it was no longer possible for researchers to know the ins and outs of AI in robotics at any given time, thanks to a second boom of AI and diversification of research in the contributing technical fields of AI and robotics, from control engineering to AI. Lozano-Perez further noted that it was the “emergence of integrated approaches” directed at solving pressing issues in the robotics industry that was stimulating research.
Such an approach continues more than 30 years later. Today, MIT’s AI Laboratory is just one (albeit a leading player) of many academic- and government-funded breeding grounds in AI and robotics, including for industrial applications. MIT researchers in 2015 published a new assembly algorithm for autonomous robots that reduces robot teams’ planning time when working in new environments. Another MIT team created a new robotic model for robotic grippers in predicting and adapting to the external force needed to grasp an object in the environment (as depicted below).
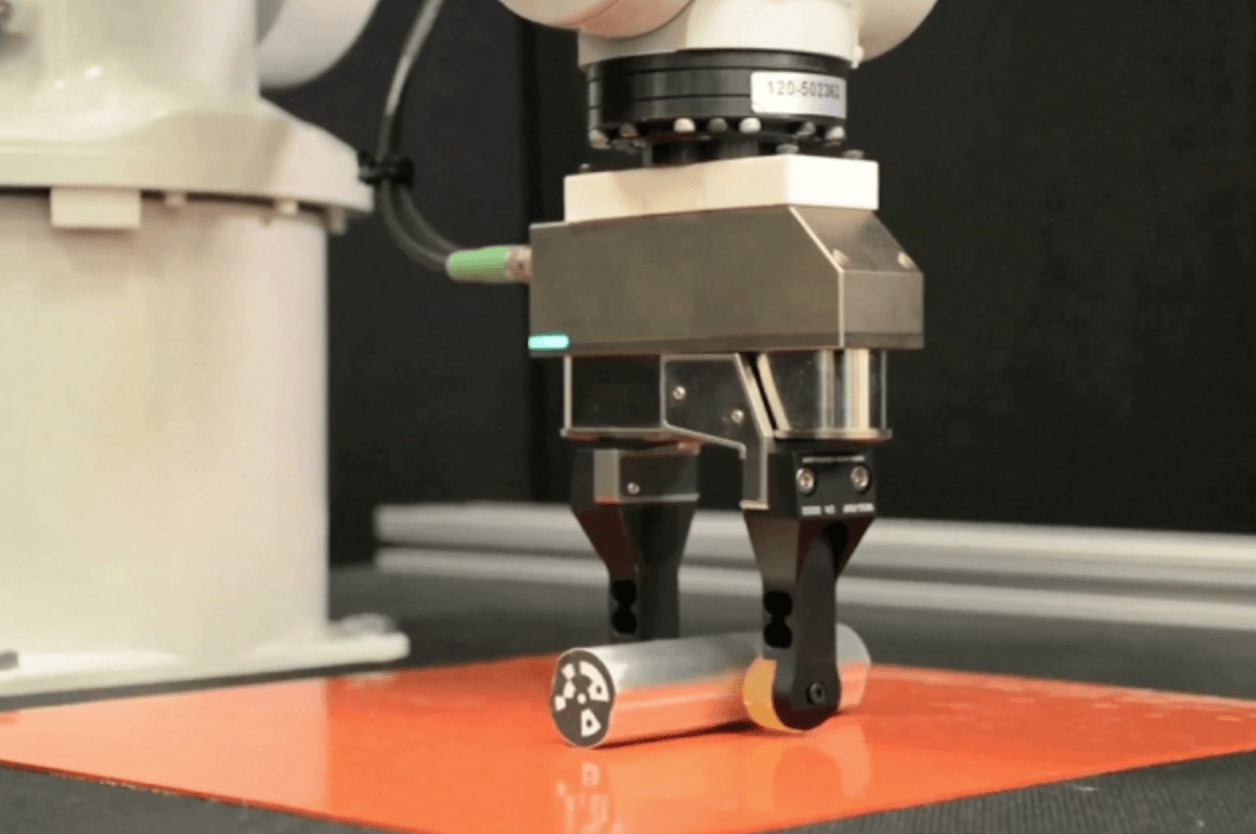
Competition Heats Up Between Major Economies
Progress has not been lost on any major competitive economy, particularly in some developing countries. A 2016 report by the International Federation of Robotics (IFR) predicts that the number of industrial robots in use globally will grow to about 2.6M units in 2019. According to IFR, about 70% of industrial robots in use today are in the automotive, electronics, and machinery industries, with electronics seeings the strongest growth rate of 18% in 2015.
On a global scale, China appears to be the most bullish. In its most recent 13th five-year-plan (2016-2020), General Secretary Xi Jinping notes “intelligent manufacturing and robotics” as a key priority for super-sized growth in China by 2030. In May of last year according to the U.S.-China Economic and Security Review Commission, China’s National Reform and Development Commission (NRDC) also announced an AI Three Year Implementation Plan, with plans to accelerate China’s AI technology and integrate big data and cloud computing networks.
All of these initiatives contribute to IFR’s predictions of an average increase in China of 20% in total industrial robot sales, amounting to more than 400,000 units in 2019. In the IFR’s report, Korea and Japan came in second and third, respectively, as of 2016 for world’s largest market for industrial robotics. USA ranked as the fourth largest market for industrial robots, with the total number of industrial robots at 36,000 units in 2015 and a predicted average growth rate of between 5% and 10% between 2016 and 2019 across all of North America. Economists, researchers, and the media have expressed concern in the growing gap of funding for industrial robotics between Chinese and U.S. governments.
According to a February 2017 article in The New York Times, while the U.S. is a leader in producing some of the most cutting-edge technology in robotics—including in collaborative and surgical technologies— much of it is being deployed overseas and there is less acceleration of application in U.S. factories as a whole than in China. Dieter Ernst, a senior fellow at the East-West Center, stated in the article: “What we can learn from the Chinese example is that the government plays a nurturing and fostering role for developing the robotics industry. We can do the same. We must do the same.”
Selected Case Studies — AI Industrial Robotics
The continued rise of industrial robots certainly seems to be an inevitability being driven by a variety of production demands, including the need for safer and more “simplified” robotic technologies to work in collaboration with humans, increased resource efficiency, and continued adaptation to the proliferation of automation and the IoT. In an effort to shine light on current initiatives in U.S.-based companies (leveraging robotics and AI technology stemming from the U.S. and other countries), we’ve highlighted the following case studies as a small sampling of how industrial robotics is helping transform industries of all sizes:
1 – Robotic Assembly of Aircraft Engine Components (Boeing)
Combining laser metrology and a real-time control system, the UK’s Manufacturing Technology Centre pioneered robot technology that enables real-time corrections to a robot’s path during the manufacturing process, particularly useful in complex manufacturing spaces like automative and aerospace industries. In 2014, Boeing began using this technology as part of a new, advanced manufacturing process for building its 777 fuselages. In the video below, you’ll see the robotic collaborators come into play around 1:35 in the video feed:
Aviation-News.net
The robotics assembly technology was put in place to increase product quality and employee safety. Known as Fuselage Automated Upright Build, or FAUB, the manufacturing process has gotten mixed reviews, as reported by The Seattle Times.It doesn’t seem too surprising that massive industry disruption is causing some obstacles, which seem to be present in the both the supply and assembly of the robotics technology. While the imperfect system has led to production delays, the company is committed to taking incremental steps to continue improving the application of the FAUB system and smoothing production flow.
2 – Packaging Commercial Products (Praxis Packaging Solutions)
Boston-based Rethink Robotics is well known for its Baxter & Sawyer industrial robots, able to be deployed and used in a variety of automated and collaborative manufacturing environments. Grand Rapids-based Praxis Packaging Solutions rolled out Baxter into its packaging and repackaging assembly lines in 2014 and 2015:
In an interview with Chris Hager, Praxis’ IT manager, he states that Baxter was employed to add value to the company’s mission of fast, cost-effective packaging and repackaging of new products and rapid reconfiguration of the assembly process. The early challenge with Baxter was setting up one task, then moving the robot to another point and setting up the next. As a solution to this problem, Rethink introduced “Landmark markers“, which use a robot positioning system and allow actions to be saved at various locations along the assembly route. This added technology greatly simplified Baxter’s operation and, according to Hager, makes it as easy to use as a tablet computer.
3 – Customized, Open-Source Robotics in Agriculture (FarmBot)
The next example is one that distances itself from big, global competition of mass production and puts power into the hands of the individual. It may be that the next emerging trend in industrial robotics is customized and open-source machines, made at scale but inspired by the “buy/grow/make local” movement. The FarmBot Genesis, described by its small production company as “humanity’s first open-source, CNC farming machine”, can even be built and coded by extreme do-it-yourselfers. The bot was designed to optimize and automate small-scale agriculture—growing seeds, weeding, and ensuring optimal growing conditions around-the-clock.
Image credit: TheManufacturer.com